お客さまと【仕組み化】の威力を実証
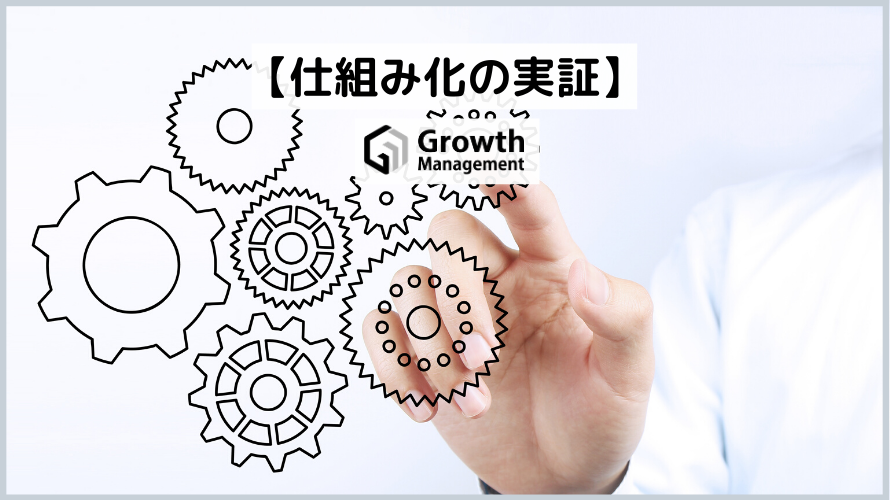
はじめに
日本の生産性は先進国最下位。最重要課題は生産性向上。働き方改革を推進せよ。と叫ばれてますが一体何をやったら良いのか。
すでに大量生産の時代は終わりましたが、かつて日本の製造業が培ってきた仕組み化の考え方はどのような業界にでも転用が利くと思ってます。
今回はビジネスチェアを大量に組み立てる事例を用いて、作業の仕組み化を細かく説明してみました。
仕組み化に特化したキャリア
まず私のファーストキャリアについて書きます。98年に某大学の工学部機械工学科を卒業、同級生が大手の自動車メーカーや電気メーカーに進む中、30名弱のベンチャーに就職しました。
私が選んだ会社はINCS。光造形装置(今で言う3Dプリンター)(確か当時6000万とか?)で主に自動車、家電メーカー向けの試作をビジネスの柱にしていた会社でした。
3DCADの研修を受けて志願したのは社運を賭けた高速金型研究室。当時の光造形技術では材料の違いによる強度不足等の課題もあり、同材質で部品を試作する高速金型はニーズがありました。
通常1型45日かかる金型製造を7日で作るというチャレンジ。納期短縮の見立てはこんな感じでした。
45日÷3稼働÷2倍速=7.5日
つまり24時間稼働して、2倍以上のスピードで働けば良いという考え方。新しいことを成すための目標設定の考え方は現状の積み上げではなく、こういった視点で考えることはとても大切だと思います。
徹底的に業務を標準化する
とは言っても24時間働きつづけることはできませんし、職人さんを大量に採用することもできないので、タスクの細分化し各タスクの必要スキルレベルを下げ、マニュアルを整備し、誰でもできるようにする。仕組みを作ったうえでリソースを投入する。こういったことが求められます。
全てのタスクは判断(2割)と作業(8割)に分けられ、判断は頭を使うこと、作業とは頭を使わなくてもできること。パレートの法則ですね。
一子相伝で受け継がれてきた金型職人さんの技術を習い、全て自分たちでやってみて、マニュアルを整備し、誰でも働くことができる工場を作り込んでいきました。ここが根本。
初期状態を把握する
現状のヒアリング
話を戻しまして、ビジネスチェア組み立ての話。
当日現場入ると、60脚ほどのうち3脚はすでに組み立てられていたので組み立てたメンバー(Aさん)に聞いてみました。
これ大変ですよねー、3脚でどれくらいかかりました?
1脚15分から20分くらいですかね。六角で手が痛くなるので連続3脚が限界でした。
・一人で組み立てるとだんだん減速する(平均17分/脚)
・課題は六角のネジまわし
組み立て手順を把握する
私たちが入ったことで、もう少し作らないと座るところがなかったので同行した他のメンバー(Bさん)が作り始めました。時間はそんなに変わらず。そこで発見した課題は以下です。
・ネジは4種類(皿×10本、短×4本、中×6本、長×4本)
・肘掛取付にフールプルーフは無し
・座面取付にもフールプルーフは無し
・寝っ転がってネジまわししてる
※フールプルーフ=誤取付防止設計
なるほど、ネジは1脚作るのに24本、つまり3脚で72本取り付けたら手が痛くなるわけだ。電動ドライバ(@3000円程度)を投入した方が良いですね。
肘掛は取付方向を前段取りで決めておけば間違えない。
寝っ転がって=これは取り付ける手順を組み替えれば解消されるはず。
工程を設計する
電動ドライバーを調達して、私も一つ作ってみることにしました。やっぱり自分でやってみるのが一番理解が進みます。そして大量生産を前提にした段取り工程と組み立て工程を設計しました。
前段取り工程
組み立てる前の工程はとても重要です。実際の組み立て工程が滞りなく進めるよう準備を進めます。
手順は以下の通りです。
1.箱の向きを揃える
2.カッターで工の字にテープを切る
3.箱のフラップ×4方向を折り曲げる
4.肘掛×2を取り出す(以後左右に分けて平積みする)
5.背もたれを取り出す(以後平積みにする)
6.座面を取り出す(以後裏返して平積みする)
7.脚中心部品を取り出す(以後まとめておく)
8.脚構成部品を取り出す(以後開梱工程へまとめておく)
9.ネジを分別する
途中発生した梱包材は決められた場所に片付ける
組み立て工程
ビジネスチェアを一つを作る工程ではなく、大量に作るために工程を明確にし、各工程の作業者が集中できるように考えていきます。
1.脚アッセンブリを組み立てる
2.座面サブアッセンブリを組み立てる
3.座面に肘掛を取付ける
4.座面に背もたれを取付ける、座面アッセンブリとなる
5.脚ASSYと座面ASSYを合体する
作業環境を整える
工程の流れを考慮した、部品保管場所(Input)、作業性・作業スペース(Process)、完成品保管場所(Output)も合わせて検討しました。
いざ組み立て開始
ターゲットは12脚。さて1脚あたりの制作時間はどれくらいか、チャレンジ開始です。リードタイム1/2くらいには短縮したいですねぇ。
作業者と役割
私:前段取り&在庫・流量を管理、指示出し
Aさん:途中段取り&在庫担当
Bさん:各作業担当
脚アッセンブリを組み立てる
・コア(黒い星型部品)に脚(銀色×5本)を仮組みをして裏返しておく
・ドライバ作業者であるBさんの左側(右利きのため)にビスをストック(ビスの種類を判断させない)
<改善案>
・各脚にタイヤを予め組み付ける前工程を作る
・予めネジをネジ穴にセットすることができる

座面アッセンブリを組み立てる
・クッションを裏返し、取付部品と向きを合わせておく
・前工程で出た改善案である予めネジをネジ穴にセットを運用し始める
<改善案>
・前工程のビニールゴミは片付けられる

座面アッセンブリに肘掛を取付ける
・前段取りとして座面に肘掛けを手動ドライバーでネジで仮止めしておく
<改善案>
・空中になっているとバランスが悪い作業効率が落ちる
→空き段ボールによる治具を作った方が良い
・Aさん担当の仮止め工程の流量が本工程の流量に追いつかず停滞した
→私が一時的に入り流量の平衡を維持した
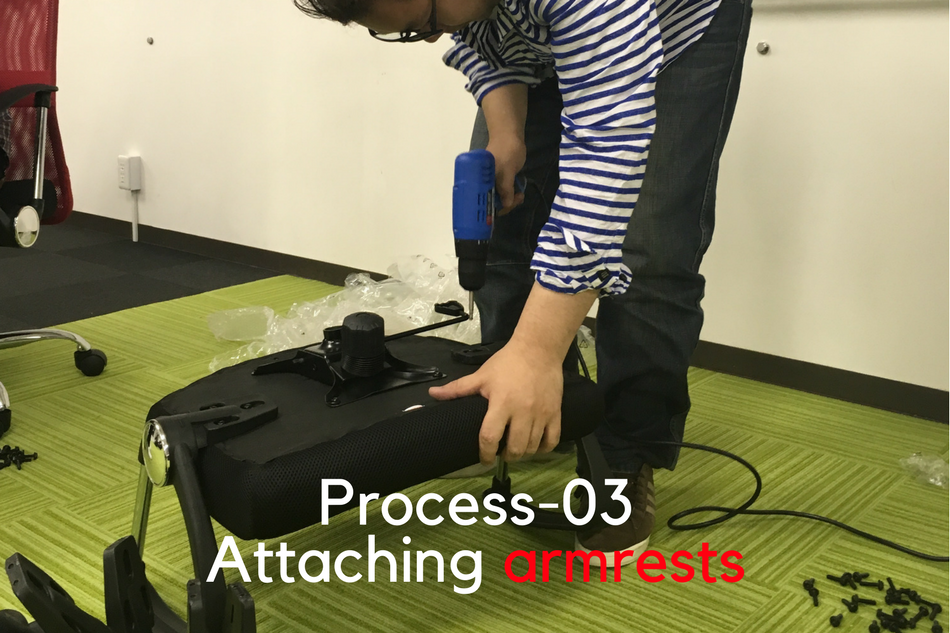
中間在庫①
キレイに隙間なく並べることで限られたスペースで在庫を管理することができます。また前工程の生産出力=中間在庫数が常に見える化できています。

座面ASSYに背もたれを取り付ける

中間在庫②
まだ脚のついていないイスたち。背筋が伸びて凛々しく見えます。
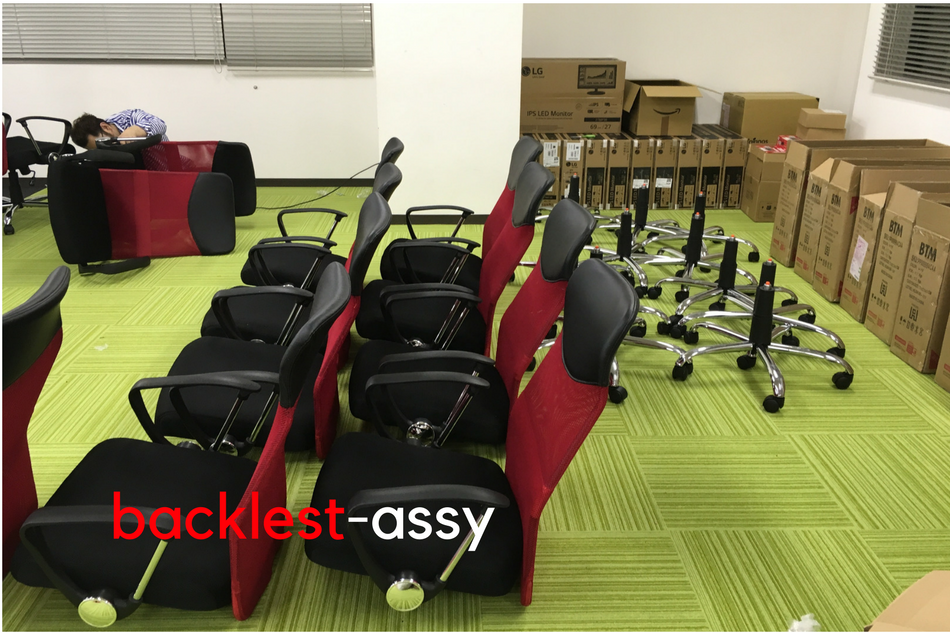
脚アッセンブリと座面アッセンブリを合体して完成
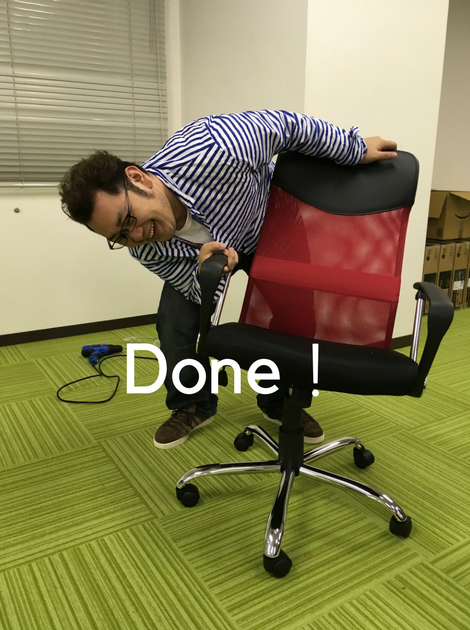
写真は1号機完成時、全力で喜びを表現していただきました!
さいごに
80分間で12脚≒6.7分/脚
うん、なかなかの成果が出ましたよ。
初期値:17分/脚
目標値:8.5分/脚(半分)
実績値:6.7分/脚
60%削減!!!
久々に興奮してしまいました。やっぱり私はこういうこと好き!
以上、ビジネスチェア制作を仕組み化により生産性の向上を実証したお話でした。
※ALTPLUS高知の代表藤田さんにご協力いただきました!
-
前の記事
超簡単!明解!【業務フロー】の書き方 2020.05.01
-
次の記事
【業務標準化】のメリットとその進め方 2020.05.12